Here in sunny Southern California, we don’t often give much thought to sump pumps. But when unexpected heavy rains arrive or flooding occurs, these unsung heroes become our homes’ best friends. Whether you’ve got a classic slab foundation or one of those quirky crawl spaces, a sump pump is your first line of defense against unwanted indoor swimming pools.
Although we enjoy mostly sunny days in Southern California, we are not immune to occasional and often unexpected storms which may lead to flooding. Underground water sources and even overzealous irrigation from neighboring properties can also pose threats. That’s where your trusty sump pump earns its keep.
Like any hardworking household appliance, sump pumps inevitably face wear and tear from constant use over the years. The ceaseless duty of pumping water away from your home’s foundation can certainly take its toll on these trusty devices. That’s why it’s so important for homeowners to stay vigilant and familiarize themselves with common sump pump issues before problems escalate.
In the following sections, we’ll examine some of the most frequent sump pump difficulties you may encounter as a homeowner. You’ll learn to identify the warning signs indicating something may be amiss, from strange noises to decreased pumping power. We’ll also cover simple methods to keep your unit in top shape year-round and when it’s best to call in the experts.
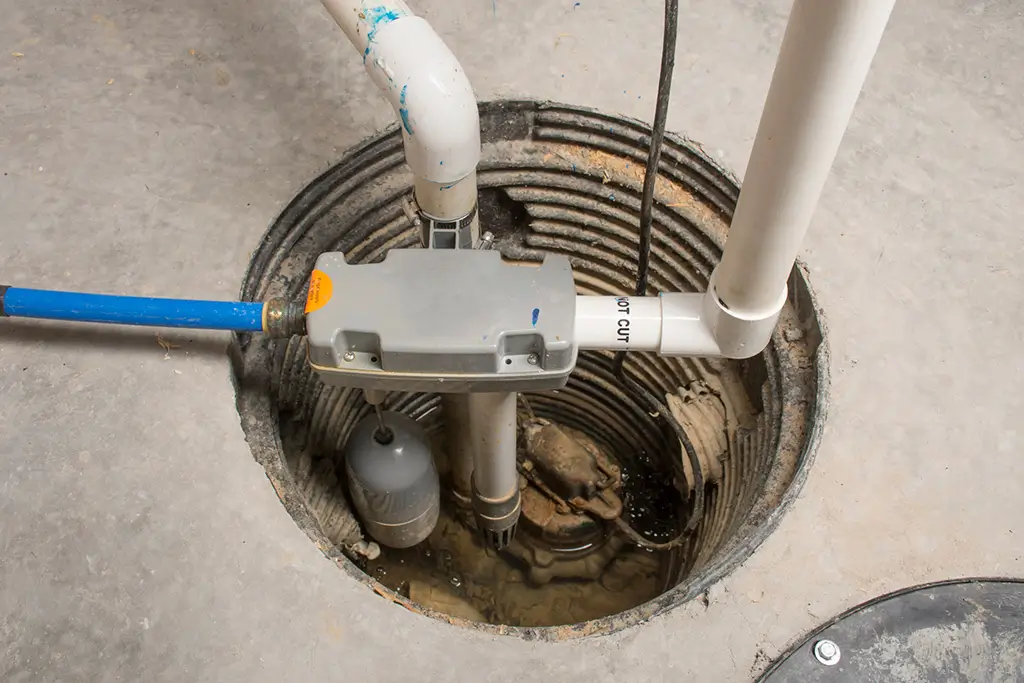
Sump Pump Basics
Before we dive into the nitty-gritty of sump pump issues and repairs, let’s cover the fundamentals. For those scratching their heads wondering “what exactly is a sump pump?”, here’s a quick rundown.
At its core, a sump pump is essentially a compact pit or basin found in basement floors or crawl spaces that collects any excess groundwater that accumulates around your home’s foundation. The pump itself is a small, hard-working motor that automatically kicks into gear whenever water levels rise inside that sump pit. Its job is to pump that water back safely away from your home through discharge pipes and out to a storm drain or dry well.
These unassuming devices may not look like powerhouses, but they play a crucial role in protecting homes from potential flooding and water damage emergencies. That’s especially true for homeowners here in Southern California. While we may not deal with torrential downpours quite like other parts of the country, our region can still experience heavy rainfall, flash floods, or steadier precipitation from atmospheric rivers at times.
When those wet conditions strike, even a modest amount of accumulated groundwater can quickly turn into a backed up, leaky mess inside your basement or crawlspace if you lack a functional sump pump doing its job. Without this first line of defense continually pumping rising water away, moisture inevitably finds its way through foundation cracks and seeping inside – bringing potential mold, mildew, and even structural issues along with it over time.
That’s why most homes and buildings constructed in our region have sump pump systems installed from the get-go. They provide an automated, hands-off way to mitigate flood risks by expelling excess groundwater before it ever has a chance to cause damage inside your home’s lower levels. Just one more way to stay ahead of potential headaches caused by our occasionally unpredictable SoCal storm seasons!
Common Sump Pump Problems
1. Power Failures
Whether from regional outages during storms or electrical issues within your home’s system, power failures render sump pumps completely useless. With no electricity flowing, these critical pumps have no way to operate and remove accumulating groundwater.
The simplest solution for this is installing backup battery packs that temporarily take over pumping duties when outages strike. For prolonged power losses, a gas-powered portable generator or hardwired standby generator provides longer-term backup power to keep your pump chugging along. It’s also wise to have your sump pump connected to a dedicated circuit to avoid overdrawing electricity.
2. Improper Installation
Problems can arise right from the start if your sump pump system wasn’t installed correctly. Improper positioning, depth and discharge setup lead to symptoms like the pump rapidly cycling on and off when it shouldn’t need to run so frequently. You may also notice water backing up or the pump seeming unable to keep up with normal accumulation despite operating constantly. Excessive operational noise, vibration or movement are other red flags of installation issues.
Having a professional inspect and potentially re-install components in a more optimal layout can solve positioning problems. Properly sizing the pump’s rated capacity to your home’s specific needs is also crucial.
3. Clogged Discharge Lines
As sump pumps operate over years of service, debris like dirt, gravel and leaves have a tendency to accumulate and clog the discharge pipe that expels water away from your home. Sediment buildup and hard water mineral deposits can further restrict water flow through discharge lines. In freezing temperatures, any moisture left inside these exposed lines risks freezing solid and fully obstructing the pipe.
Routinely inspecting and flushing out discharge lines clear potential obstructions before major clogs form. Installing a vent, check valve or small grated cover at the discharge outlet prevents pest entry. For winter operation, wrapping exposed piping with insulation material prevents freezing backups.
4. Pump Burnout
Even with proper pump sizing, continuous heavy-duty operation can severely overtax the hardworking motor and internal components over time. If the installed pump is too small or undersized for the groundwater accumulation needs of your home, it has to work exponentially harder and wears down rapidly. Pumping water loaded with heavy sediment or debris also accelerates wear.
Ensuring you have the properly rated pump capacity avoids this burnout. Installing a secondary backup pump allows you to alternate duties so each pump gets periodic rest periods. Keeping the sump pit and intake areas clear of excess sediment buildup also eases the pump’s workload.
5. Float Switch Issues
The float switch is the simple component that tells the sump pump when to activate based on rising water levels in the pit area. If this free-floating switch gets stuck in the fully raised or lowered position due to debris obstructions or tangles, it fails to accurately sense water heights. Inadvertent adjustment of the float switch height so it no longer triggers the pump at intended levels also causes problems. Using the incorrect float switch weight leads to improper buoyancy that prevents it from tracking changing water levels.
Clearing away any obstructions so the float can freely travel its full vertical range fixes most switch problems. Adjusting components like switch height and counterweight as needed restores proper activation points. Replacement is necessary for any damaged or faulty switches.
6. Sump Pit Overflows
No matter how powerful the installed pump, if the actual sump pit or basin is undersized it cannot contain normal accumulating water volumes before overflowing into your home’s basement or crawlspace. Even properly-sized pits may potentially get overwhelmed by extremely heavy rainfall or flood conditions causing excessive water entry. A lack of regular sump pit cleaning also allows debris buildup to take up space intended for water collection.
Routinely cleaning out residue buildup maximizes the pit’s holding capacity. For chronically overflowing pits, enlarging or expanding the overall pit basin area may be necessary. As a last resort, installing a secondary higher-capacity pit and pump handles extreme water backup during major rainfall events.
7. Pump Cycles Too Frequently
If you notice your sump pump kicking on in rapid cycles every few minutes when it should only need to activate sporadically, something is likely amiss. Higher than typical groundwater levels continually filling the pit trigger this excessive cycling. An undersized or underpowered pump struggles to clear normal water volumes. A failed or leaking pump check valve allows discharged water to backflow into the pit area, requiring constant re-pumping.
Assessing if a larger horsepower pump with greater rated capacity suits your home’s needs solves sizing issues. Replacing any faulty check valves prevents pumped water from re-entering the pit area. As an extra measure, pit liners and extended discharge piping move drained water further away from the foundation.
8. Loud Noises or Vibrations
While some operational noise is normal for hard-working sump pumps, excessive loud clanking, grinding or rattling indicates potential internal problems. Components like bearings, impellers and shaft seals have a finite service life and will eventually wear out, causing disruptive noises. Debris like rocks or sticks could also get caught in the pump mechanism and rattle around noisily. Buildup of sediment or mineral deposits inside the pump housing leads to internal grinding sounds as parts grind against debris.
Dismantling the pump to clean out trapped debris may restore quiet operation. Having the pump professionally inspected for worn components needing repair or replacement also eliminates excessive noise problems.
The sooner any of these common sump pump problems get addressed, the better protected your home will be!
When to Call a Professional
Even avid DIYers have to know their limits when it comes to sump pump repair projects. While basic troubleshooting and maintenance tasks are well within most homeowners’ abilities, there are certain scenarios where professional expertise is highly advised to properly diagnose and resolve more serious pump problems. Attempting overly complicated repairs yourself risks causing further damage or creating potential safety hazards if not done with the proper training and equipment.
One situation where it’s wise to promptly call in the pros? Any electrical issues impacting your sump pump’s operation. While checking for tripped circuit breakers or simple resets are reasonable DIY steps, anything involving suspected wiring faults, electrical shorts or signs of motor burnout requires an electrician’s skilled eye. Messing with electrical components improperly could potentially lead to dangerous shocks, fire hazards or making the underlying problem even worse before it gets better. When in doubt about electrical issues, putting safety first by reaching out to licensed professionals is a must.
Similarly, if your sump pump’s problems seem to stem from internal mechanical or seal failures, it’s best to have a certified plumbing technician take a look. While minor adjustments or replacing easily accessible external components like float switches can be DIY jobs, actually disassembling and working on the pump’s inner motor assemblies is a complex task requiring specialized knowledge and tools. Trying to personally repair failed bearings, impellers and shaft seals often ends up costlier in the long run than simply having an expert correctly diagnose and replace the entire pump mechanism when needed.
In some cases, sump pump problems might actually stem from installation issues never corrected by the original contractor. If adjustments like raising the pump housing, resizing discharge pipes or expanding pit basins seem necessary, a professional plumber will have the expertise to properly reconfigure the entire pump setup for optimal performance tailored to your home’s specific needs and water table levels.
And of course, any projects involving extensive excavation work to access buried sump pump components, drain tile or discharge piping clearly fall into a professional’s domain. Attempting that level of digging and subsurface work yourself risks inadvertently destabilizing your home’s foundation or causing serious property damage.
The Homeowner’s Handbook: Keeping Sump Pumps in Peak Condition
Water in all the wrong places can quickly turn your basement into a damp, musty nightmare. But your home’s unsung hero – the sump pump – prevents those soggy situations before they start. Just a little proactive pump prep work goes a long way in avoiding costly moisture damage down the road.
From cleared discharge lines and properly adjusted float switches to sizing pumps appropriately and allowing rest periods, many sump pump issues are well within most homeowners’ abilities to maintain and troubleshoot.
But there’s no shame in knowing your limits either. Whether you suspect an electrical gremlin or the pump itself is down for the count mechanically, trusted pros have the specialized tools and trained eyes to take over those bigger jobs seamlessly. Going at it alone on major repairs often causes more harm than good.
Don’t let lack of attention cause expensive headaches with preventable water damage! When upkeep goes beyond your abilities, the certified technicians at All Pro Plumbing, Heating, Air & Electrical are just a call away at (909) 500-8193. Count on their expertise to get your system back on full guard duty quickly.